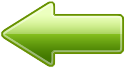
Project:
BuckRV-8 - Entry
Jan 18, 2024
3.9
L wheel pant fitting, clearance blister, and mount build-up
Category: Wheel Pants
1. Filled the tires to 40 PSI just to make sure I'm not going to affect the fit of the pants with too-low tire pressure.
2. Cross-checked some wheel pant dimensions from my friend's RV-8, just to see if mine were going to be close. As it turns out, if I follow Van's instructions precisely, the trailing edge of mine are slightly over 2" higher at the trailing edge than his. I set mine temporarily at the factory angle and stood back to see if looks OK. It looks reasonable and should give me good ground clearance, so that's what I'm going to go with.
3. Trimmed a bit more from the aft edge of the gear leg hole for better clearance.
4. Dropped a plumbob at the tail of the airplane and also at the firewall, then stretched a piece of fine string and taped it to the floor. Put pieces of tape on the floor, fore and aft of the wheel/tire. Used a square to mark perpendicular lines down to the tape from the forward side of the tire and the aft end of the wheel pant, then manipulated the wheel pant until the measurements from aircraft centerline to my tape marks were equal. Hopefully, this will get the pant right in line with the longitudinal axis of the airplane
5. Carefully duct-taped the pant into this position.
6. Back-drilled the four attach holes through the pant attach bracket and through the pant, then clecoed it in place.
7. Took note of the slight gap between the attach bracket and the lower holes on the pant, and also took note of the interference between the brake fluid bleed port and the brake line fitting and the pant. Marked both.
8. Cut out an oval area on the inboard side of the pant so the brake components will clear.
9. Scuffed and cleaned the two areas on the pant in preparation for fiberglassing.
10. Made a paper template and cut three layers of BID fiberglass, then made a sandwich layup. Applied the layup to the teardrop opening, stippled it down on the edges, then used a gloved finger on the inside to push it out into a gentle blister shape. Applied a bit more resin to the outside perimeter, then applied peel ply to the perimeter. (I didn't apply peel ply to the blister because I didn't want to risk collapsing it.)
11. Applied four or five wetted layers of 1/2" x 2" strips of fiberglass on the inside of the pant, over top of the aft attach holes. Hopefully, this will be enough of a shim for the attach bracket, once it's sanded appropriately.